Reductive Discharge Ink-Jet Printing of Pre-Dyed Textile Fabrics
CURRENT TRENDS IN FASHION TECHNOLOGY & TEXTILE ENGINEERING- JUNIPER PUBLISHERS
Authored by David M Lewis
Abstract
Bleached cotton fabrics have been dyed with Remazol (sulphatoethylsulphone (Dystar)), Procion MX (dichloro-s-triazine (Dystar)) and Procion HE (bis-monochloro-s-triazine (Dystar)) reactive dyes to yield suitable coloured backgrounds for subsequent reductive discharge ink-jet printing. Silk fabric has also been dyed with an acid dye to provide an alternative substrate for subsequent discharge printing. Suitable white discharge inks have been formulated using either Decrolin (zinc sulphoxylate formaldehyde (BASF)) or Rongalit C (sodium sulphoxylate formaldehyde (BASF)), whilst coloured illuminating inks have been formulated using either vat or solubilised vat dyes. Inks containing both a discharging agent and an illuminating colour have also been developed. A process has been developed in which the free aromatic amine groups present in the discharged areas of white prints are diazotised and coupled to a suitable aromatic amine, phenol or naphthol derivative to provide an illuminated print
Introduction
Discharge printing is a technique that is widely used in the textile industry and involves the local discharge of dye on a ground shade using a suitable chemical in a print paste [1]. Such discharge agents include oxidants, such as per-acids, or reductants, such as sodium or zinc sulphoxylate formaldehyde, the latter being more usually used. Coloured prints are also desired and so illuminated discharge pastes that contain a discharge agent and either an oxidation or reduction-resistant dye, such as a vat or sulphur dye, are extremely important.
This study concerns the ink-jet printing of reductive discharge styles on coloured backgrounds dyed with azo dyes, using inks formulated with either Decrolin or Rongalit C:
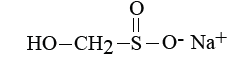
Sodium sulphoxylate formaldehyde (Rongalit C) [2].
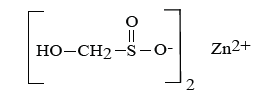
Zinc sulphoxylate formaldehyde (Decrolin) [3]. The reductive discharge process for Rongalit C may be represented by the following scheme: a. Formation of the sulphinate reducing species
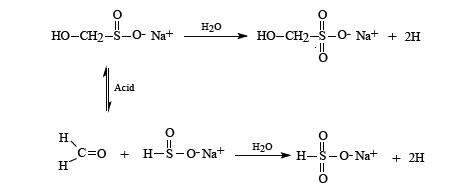
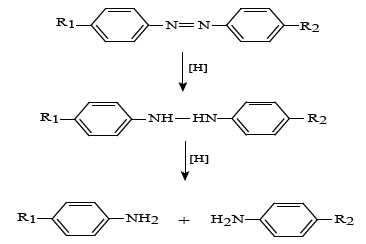
where R1 represents the solubilizing group of an azo dye and R2 other groups present in azo dye. Once the azo linkage is split the dye is decolourised and due to its small size is readily removed from the textile by a thorough washing process. This study formulated coloured discharge inks containing reduction stable vat or sulphur dyes. Such dyes are not generally water soluble but can be converted to a water soluble leuco form by treatment with an appropriate alkaline reducing agent to enable their use in ink formulations. Such processes are illustrated below. Vat dyes can be converted to their water-soluble leuco form by heating them at 50°C in an alkaline solution of sodium dithionite (hydros). The process being illustrated below: c. Formation of reducing species
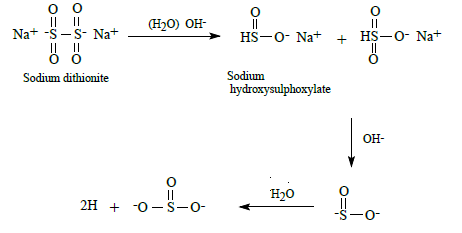
d.Reduction of vat dye to its water soluble leuco form
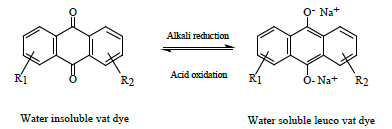
Stabilized water-soluble vat dyes (CI Solubilised Vat dyes) are commercially available in which the leuco form of the vat dye is treated with sulphuric acid to form a sulphate ester [4]. The process being indicated below:
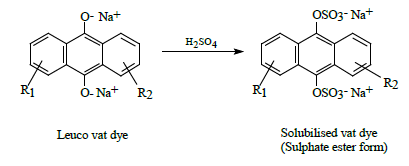
Sulphur dyes are water insoluble dyes that contain disulphide residues capable of reduction with sodium sulphide to yield a water- soluble thiolate containing dye species (leuco form). The process is demonstrated by the following scheme:
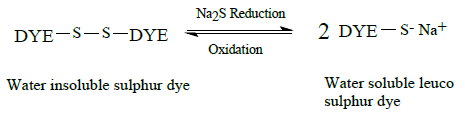
Solubilised sulphur dyes are also available in which the water insoluble sulphur dye is treated with sodium sulphite to form a water soluble Bunte salt derivative; the process occurring being given below:

Experimental
Materials
Lightweight bleached cotton fabric was supplied by Whaley’s (Bradford) Ltd. A bleached, 100% cotton fabric (156g/m2) supplied by Whaley’s (Bradford) Ltd. was used throughout the study. Commercially available reactive dyes from various dye manufacturers were studied – they included the following. The dyes used were donated by the relevant dyestuff manufacturers and are listed in the text. All other chemicals were of laboratory grade as supplied by Aldrich Chemicals (UK).
Methods
A desk-top HP 540 ink-jet printer was used to print all fabrics. Cartridges were cut open and filled with the necessary inks. Steaming to fix the ground shades and printed areas was carried out in a Mathis laboratory steamer.
Dyeing of Background Fabrics
The processes used to provide suitably dyed background fabrics for subsequent discharge printing are described below. Cotton fabrics were dyed using either a Procion MX, Procion HE or Remazol reactive dye, whilst silk fabric was dyed with an acid dye.
Dyeing of cotton with Remazol dyes
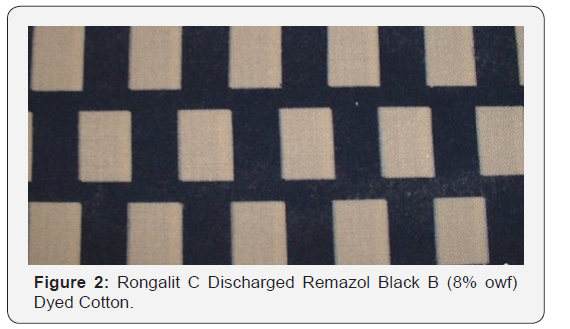
Bleached cotton (Whaleys (Bradford) Ltd) was dyed with 8% owf Remazol Black B (Figures 1 & 2) on a Mathis laboratory jig dyeing machine in accordance with the following process:
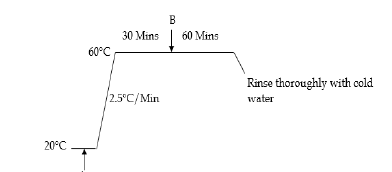
A. 8% owf Remazol Black B, 80 gdm-3 sodium sulphate, pH 7, liquor ratio 10:1, 250g cotton fabric. B. 20 gdm-3 Trisodium phosphate. The dyed fabric was soaped at 100°C for 15 minutes with 2 gdm-3 Sandoz in NIE (Clariant) to yield a deep black coloured fabric. A 4% owf dyeing of Remazol Brilliant Orange 3R was also produced on cotton in accordance with the above dyeing process.
Dyeing of cotton with Procion MX dyes
Bleached cotton was dyed green on a laboratory jig dyeing machine (Mathis) using a mixture of 3% owf Procion Yellow MX- 3R and 3% owf Procion Blue MX-2G in accordance with the following dyeing process:
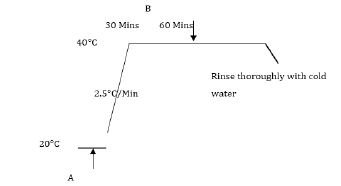
A. 3% owf Procion Yellow MX-3R, 3% owf Procion Blue MX-2G, 80 gdm-3 sodium sulphate, pH 7, liquor ratio 10:1, 250g cotton fabric. B. 20 gdm-3 Sodium carbonate. The dyed fabric was soaped at 100°C for 15 minutes with 2 gdm-3 Sandozin NIE to yield a dark green coloured fabric.
Dyeing of Cotton with Procion HE Dyes
Bleached cotton was dyed red on a laboratory jig dyeing machine using 4% owf Procion Red HE-3B in accordance with the following dyeing process:

A. 4% owf Procion Red HE-3B, 80 gdm-3 sodium sulphate, pH 7, liquor ratio 10:1, 250g cotton fabric. B. 20 gdm-3 sodium carbonate The dyed fabric was soaped at 100°C for 15 minutes with 2 gdm-3 Sandozin NIE to yield a deep red coloured fabric
Dyeing of silk with Bordeaux R (Aldrich) (CI Acid Red 17)
Silk fabric was dyed with 4% owf Bordeaux R on a Roaches Pyrotec S laboratory dyeing machine in accordance with the following process:
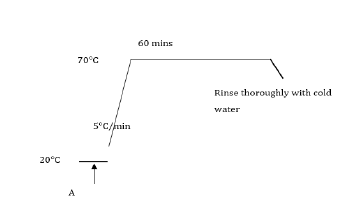
A. 4% owf Bordeaux R, 3% sodium acetate, pH 4.5, liquor ratio 10:1, 5g silk fabric. The dyed fabric was soaped at 70°C for 15 minutes with 2 gdm-3 Sandozin NIE to yield a deep red coloured fabric.
Formulation of Printing Inks
The formulation of inks suitable for ink-jet discharge printing is described below. Inks capable of producing a white print on a suitably dyed background may be formulated using a reducing agent, such as Decrolin or Rongalit C, which acts by destroying the azo linkage in the background dye to yield a colorless area. Inks capable of producing illuminated prints in which the white discharged areas are re-dyed may be formulated by incorporating a discharge resistant dye, such as a vat or solubilised vat dye, in the discharge ink formulation. The formulation of inks containing both an illuminating dye and a discharge agent may result in inks of low aqueous solubility, which may exhibit cartridge blocking problems and poor long-term aqueous stability. One way of eliminating such a problem is to develop a system in which the background fabric is initially inkjet printed with an ink containing the discharge agent and then over-printed in a second step with an ink that contains an illuminating dye.
Reductive Discharge Inks
White Reductive Discharge Inks: A white discharge ink was formulated by dissolving Decrolin (150 gdm-3) and diethylene glycol (150 gdm-3) in distilled water; the ink having a pH value of 4.2 (subsequently this ink was adjusted to pH 6 without affecting the discharge efficiency). The ink was filtered through a Whatman No1 filter paper and added to a black HP 540 ink cartridge. A second white discharge ink was prepared as above, but in this case Rongalit C was added in place of Decrolin as the reducing agent; the ink demonstrating a final pH value of 11.0
Coloured Reductive Discharge Inks: Coloured discharge inks were formulated using Rongalit C and either a vat or solubilised vat dye in accordance with the following ink formulations: a. Yellow discharge ink 4g Parkosol Golden Yellow IGA (CI Solubilised Vat Yellow 4). 20g Rongalit C. 20g Diethylene glycol. 56g Distilled water a. Blue discharge ink 4g Indigosol Blue IBC (CI Solubilised Vat Blue 6) 20g Rongalit C 20g Diethylene glycol 56g Distilled water b. Red discharge ink 4g Indigosol Brilliant Pink I5B (CI Solubilised Vat Red 9) 20g Rongalit C 20g Diethylene glycol 56g Distilled water c. Red discharge ink 4g Caledon Red 3B (CI Vat Red 10) 20g Rongalit C 10g Diethylene glycol 5g Sodium hydroxide 4g Ufoxane 2 57g Distilled water
The inks were filtered through Whatman No1 filter papers and added to black HP 540 ink cartridges. Attempts to formulate inks containing Decrolin as the discharge agent proved unsuccessful due to the zinc ions present in the ink formulation causing precipitation of the temporary solubilised vat dyes.
Coloured illuminating inks: Coloured illuminating inks were formulated using either a vat or solubilised vat dye in accordance with the following ink formulations:
Yellow illuminating ink
4g Parkosol Golden Yellow IGA (CI Solubilised Vat Yellow 4) 96g Distilled water
Blue illuminating ink
4g Indigosol Blue IBC (CI Solubilised Vat Blue 6) 96g Distilled water
Red discharge ink
4g Indigosol Brilliant Pink I5B (CI Solubilised Vat Red 9) 96g Distilled water
Red illuminating ink
4g Caledon Red 3B (CI Vat Red 10) 2g Sodium dithionite 2g Sodium hydroxide 2g Ufoxane 2 90g Distilled water
Blue illuminating ink
10g Indigo (CI Vat Blue 1) 30g Sodium dithionite 8g Sodium hydroxide 10g Ufoxane 2 42g Distilled water
Green illuminating ink
4g Sulphur Liquid Green QGFC (CI Leuco Sulphur Green 2) 96g Distilled water
Ink formulations (iv) and (v) were heated at 50 °C for 5 minutes, cooled to room temperature and milled on a laboratory Eiger mill for 1 hour. The inks generated were filtered through Whatman No1 filter papers and added to black HP 540 ink cartridges
Discharge Printing Process
White Discharge Prints
White discharge prints on reactive dyed cotton fabrics: Dyed cotton fabrics were stuck to A4 pieces of paper with double sided tape and printed on a HP 540 Deskjet printer with an ink cartridge containing either the Decrolin or Rongalit C discharge ink. The sample was fed through the printer twice and then removed from its paper backing. The sample was steamed at 104°C (saturated steam) on a Mathis laboratory steamer for 10 minutes. After steaming, the sample was washed thoroughly with cold water to yield a white print on a coloured background. The fabrics printed with Decrolin based inks (pH 6) produced whiter discharge areas than the corresponding prints obtained using Rongalit C based inks (pH 11). Under the alkaline conditions present for the Rongalit C discharge inks, the aromatic amines covalently attached to the fabric after discharge exist in an unprotonated form and may be readily oxidized in the air to form off-white oxidation products. In the case of the acidic Decrolin discharge inks, the aromatic amines covalently attached to the fabric after discharge exist in a protonated form and are therefore less readily oxidized in the air to give off-white products. Thus, Decrolin based discharge inks appear to provide the most suitable method of producing stable white prints on a previously dyed cotton substrate.
White discharge prints on acid dyed silk fabrics: Acid dyed silk fabrics were mounted on paper and inkjet printed with a Decrolin based ink formulation. The prints were steamed at 104°C for 10 minutes, rinsed with cold water and finally soaped at 70°C with Sandozin NIE (2 gdm-3) for 15 minutes. The resulting samples exhibited a white print on a red background.
Illuminated Prints on Cotton Fabrics
Illuminated prints on dyed cotton backgrounds (twostep process)
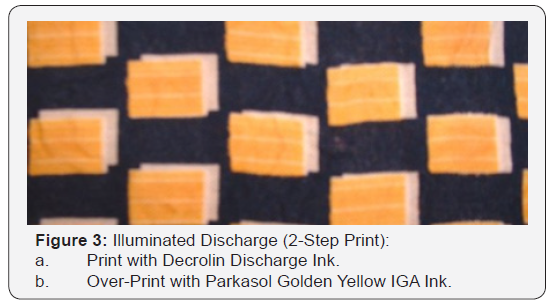
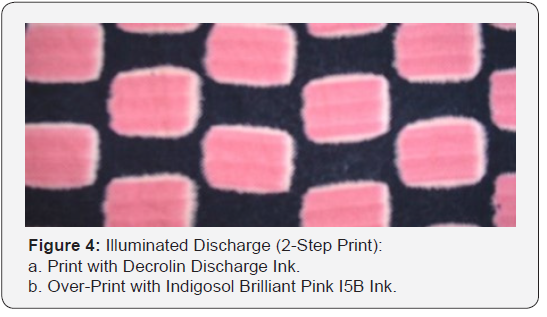
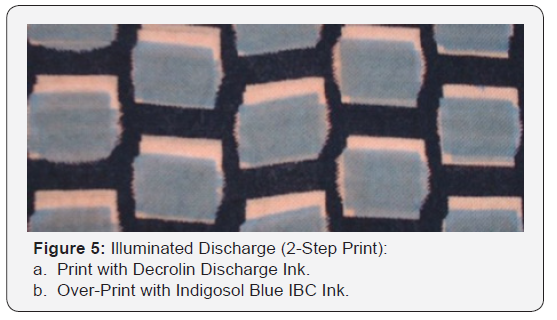
Remazol Black B (8% owf) dyed cotton fabrics were initially inkjet printed with an ink containing Decrolin as a reducing agent and then over-printed with an ink formulation containing either a vat or solubilised vat dye as an illuminating colour. The print was steamed for 10 minutes at 104°C and the print then added to an oxidising bath (200 ml) containing sodium nitrite (0.25g) and concentrated sulphuric acid (0.5g) to yield a subsequent fabric which exhibited a coloured print on a black background (Figure 3-5). The above process was repeated, but in this case the discharged area was over-printed with an illuminating ink formulation containing Sulphol Liquid Green QGCF (a leuco Sulphur dye) rather than a vat dye. The discharge was promoted by steaming at 104 °C for 10 minutes and the illuminating dye developed in a bath (200 ml) containing hydrogen peroxide (1 gdm-3). A black fabric containing a green print was achieved.
Illuminated Prints on Dyed Cotton Backgrounds (One- Step Process)
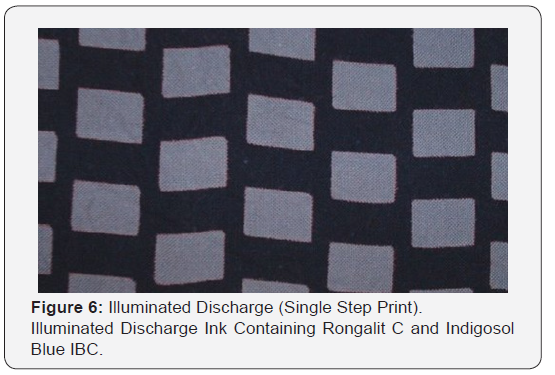
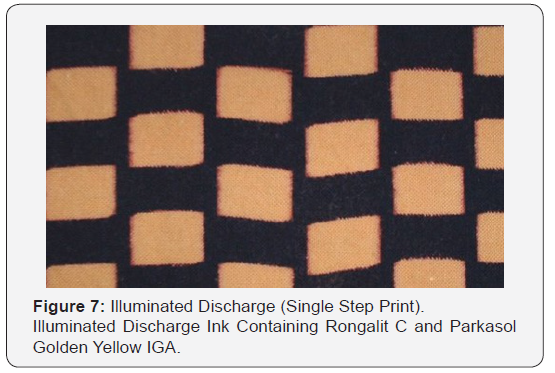
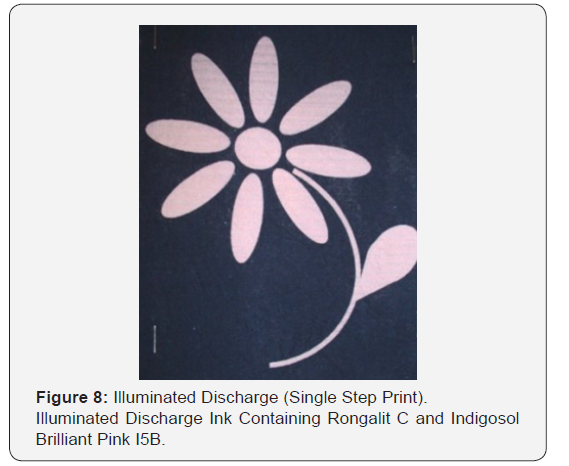
Remazol Black B dyed cotton fabrics (8% owf) were inkjet printed with ink formulations containing both a solubilised vat dye and Rongalit C; the printed fabrics being steamed at 104°C for 10 minutes to activate the discharge process. After steaming, the prints were treated in an oxidising bath (200 ml) containing sodium nitrite (0.25g) and concentrated sulphuric acid (0.5g) to yield a subsequent fabric which exhibited a coloured print on a black background. The prints were thoroughly washed with cold water and finally soaped at the boil with Sandozin NIE (2 gdm-3) for 15 minutes. The prints demonstrated a slight haloing effect due to the reducing agent (small molecular size) diffusing more rapidly than the illuminating dye. Pre-treating the background fabric with a thickening agent prior to ink-jet printing may eliminate such problems. Thus, the background fabric was padded on a Mathis laboratory padder with an aqueous solution of a thickening agent containing either CHT Alginat MV (CHT, 40 gdm-3), CHT Alginat EHV (CHT, 40 gdm-3) or Cellcosan 2000 (Noviant BV, 40 gdm-3); the fabric being padded so as to achieve a wet pick-up of 100%. The padded fabrics were dried at 100°C for 3 minutes prior to inkjet printing. Illuminated discharge prints obtained on background fabrics pre-treated in this manner exhibited no haloing effects and showed enhanced print definition and clarity (Figure 6-8).
Diazotisation and Coupling of Covalently Bound Amines
Remazol Black B (8% owf) dyed cotton fabrics were inkjet printed with discharge inks containing Decrolin and the subsequent fabrics steamed at 104°C for 10 minutes to yield white prints on a black background. The prints were thoroughly washed with cold water and the free aromatic amine residues present within the white discharged areas of the fabric diazotized in an ice cold aqueous solution of nitrous acid (150 ml); nitrous acid being formed in situ via the addition of sodium nitrite (0.9g) to an aqueous solution of concentrated hydrochloric acid (1g). The diazotized fabrics were washed with ice cold water and the fabrics placed for 5 minutes in an aqueous solution (100 ml) of either 2-naphthol-3,6-disulphonic acid (1g), H-acid (1g) or p-cresol. The fabrics were rinsed with cold water and soaped at the boil with Sandozin NIE (2 gdm-3) for 15 minutes to yield either an orange, red or yellow print on a black background. The process may be summarised by the following scheme:
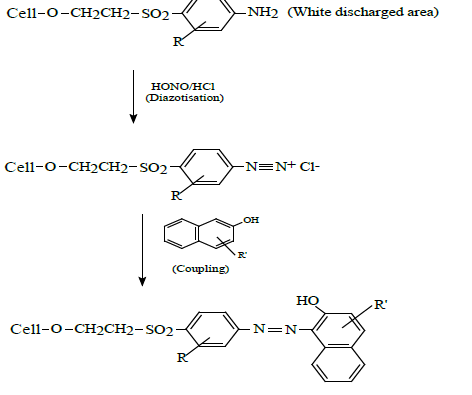
Wash-Fastness Properties of Illuminated Discharge Prints on Dye Cotton Fabrics
Remazol Black B (8% owf) dyed cotton fabrics were discharge printed with red, yellow and blue inks containing Rongalit C and ether CI Solubilised Vat Red 9, CI Solubilised Vat Yellow 4 or CI
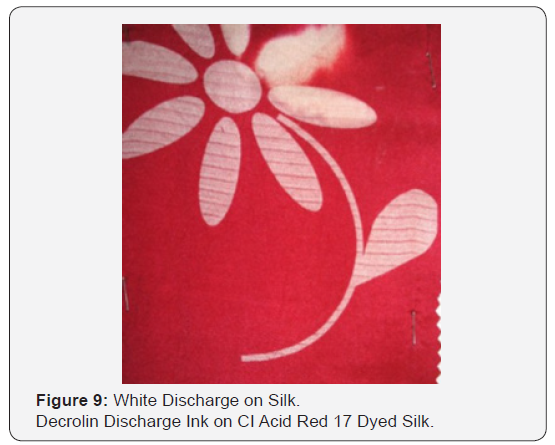
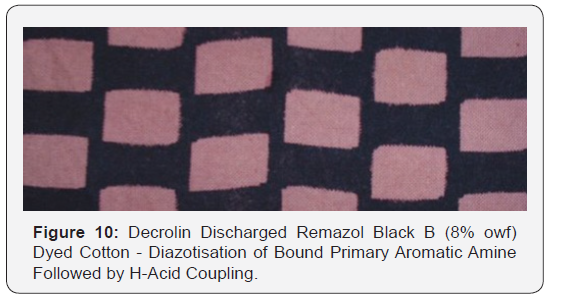
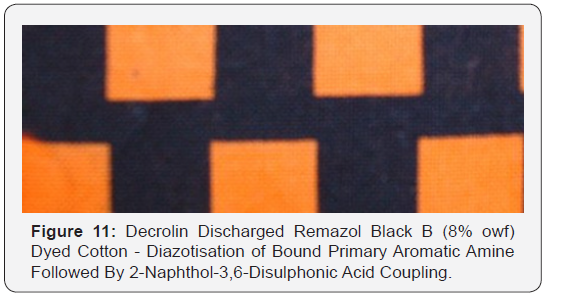
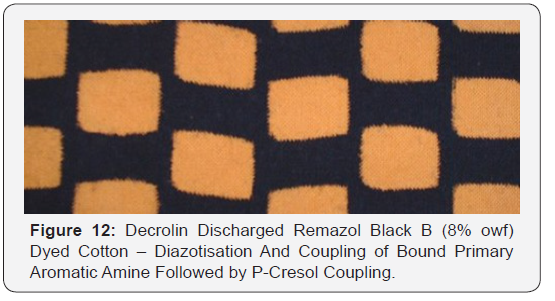
Solubilised Vat Blue 6. The fabrics were steamed at 104°C for 10 minutes to yield red, yellow or blueprints on a black background (Figures 9-12). The resulting prints were rinsed with cold water and then subjected to ISO 3 wash-fastness tests. The ISO 3 wash-fastness test involves treating a 10 x 4 cm sample of fabric and an adjacent multi-fibre strip at 60°C for 30 minutes in an alkaline soap solution containing soap flakes (5 gdm-3) and sodium carbonate (2 gdm-3). The wash-fastness of the dyed fabric can then be determined by assessing the change in shade of the dyed fabric after washing and by assessing any staining occurring on the adjacent multi-fibre strip. The wash-fastness test showed that all three coloured prints lost colour on soaping, which resulted in the staining of the nylon 6,6 and secondary cellulose acetate fibers present in the adjacent multi-fibre strips (Figures 13-15). This did not happen with those prints developed by the diazotisation (nitrous acid) and subsequent coupling (aromatic phenol, amine or naphthol derivative) of the discharged white ground areas. In such cases, the illuminating colour was covalently bound to the substrate and so exhibited excellent wash-fastness properties; the wash-fastness being like a conventional reactive dyeing on the substrate.
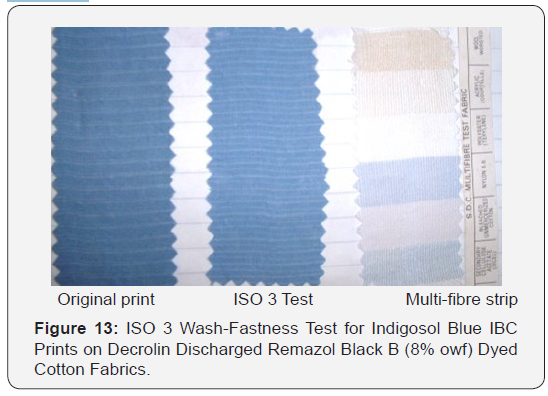
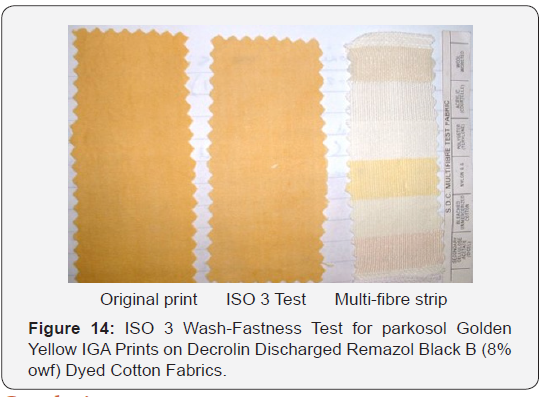
Conclusion
Discharge inks containing either Decrolin or Rongalit C can be prepared and readily ink-jet printed on pre-dyed background fabrics using an office ink-jet printer. The printed fabrics can then be steamed to produce white images on a coloured background. The images achieved using Decrolin appeared whiter than the corresponding images obtained using Rongalit C; both sets of prints gradually yellowing on storage. The cartridges containing the discharge agents were repeatedly used over several weeks without any loss of performance or evidence of print head blocking. Coloured discharge inks can be formulated which contain both a discharge agent and a solubilised or leuco vat dye; such inks enabling the production of coloured images on a coloured background. Rongalit C appeared to be the most suitable discharge agent as it enables water soluble inks to be readily formulated. If Decrolin was added to the coloured ink formulation, then the zinc ions present either caused the immediate precipitation of the vat dye present or resulted in an ink of short storage stability. As an alternative to vat dyes, solubilised Sulphur dyes may also be used as illuminating colors in discharge ink formulations. Illuminated images may also be achieved via a two-step process in which the background dye is initially printed with a white discharge ink formulation and then over-printed with an ink formulation containing either a solubilised vat or Sulphur dye. Such a process would enable both Decrolin and Rongalit C to be present in the discharge ink formulation.
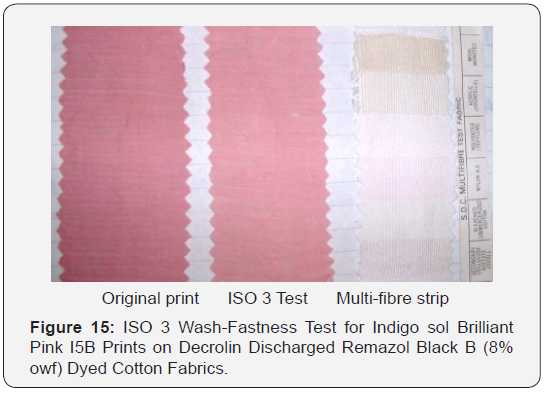
Ink-jet cartridges containing solubilised vat dyes were found to suffer from print head blockage problems after several days due to the dye on the print head surface gradually oxidizing back to its water insoluble form on air exposure. Illuminated prints achieved using a colored discharge formulation exhibited haloing effects in which a white discharged area was found to encircle the colored area. By pre-treatment of the fabric with a suitable thickening agent, such effects could be eliminated and an improvement in print definition and clarity achieved. Single colored prints under a dark background of a different colour can be produced by diazotising the covalently bound primary aromatic residues present in the discharge area and coupling them to a suitable aromatic amine, phenol or naphthol derivative. In the case of solubilised vat dyes, ISO 3 wash-fastness tests carried out on illuminated discharge prints indicated that some loss of dye from the illuminated area had occurred; the tests also indicating that significant staining of adjacent nylon 6,6 and secondary cellulose acetate had occurred. However, in the case where colour was developed by diazotising and coupling, excellent wash-fastness properties were exhibited.
To Know More About Current Trends in Fashion
Technology & Textile Engineering Please click on:
https://juniperpublishers.com/ctftte/index.php
Comments
Post a Comment